Abstract
Vanguard Automation's fully automated technologies like Photonic Wire Bonding and facet-attached micro-optical elements are advancing photonic integration and packaging. Their solutions enable seamless transitions from prototyping to volume production.
Introduction
The rapid pace of innovation in photonic integrated circuits is increasing the need for faster, more scalable solutions. Vanguard Automation aims to accelerate photonic development through fully automated nano-fabrication processes for integration and packaging. Their portfolio of technologies facilitates the transition from prototyping to high-volume manufacturing.
Enabling Scalable Photonic Integration
Vanguard’s Photonic Wire Bonding (PWB) utilizes advanced 3D nano-printing to create low-loss 3D connections between optical components. This provides design flexibility and automation. Their facet-attached micro-optical elements allow low-loss coupling and wafer-level probing. Together, PWB and faceted elements advance photonic packaging and assembly across platforms.
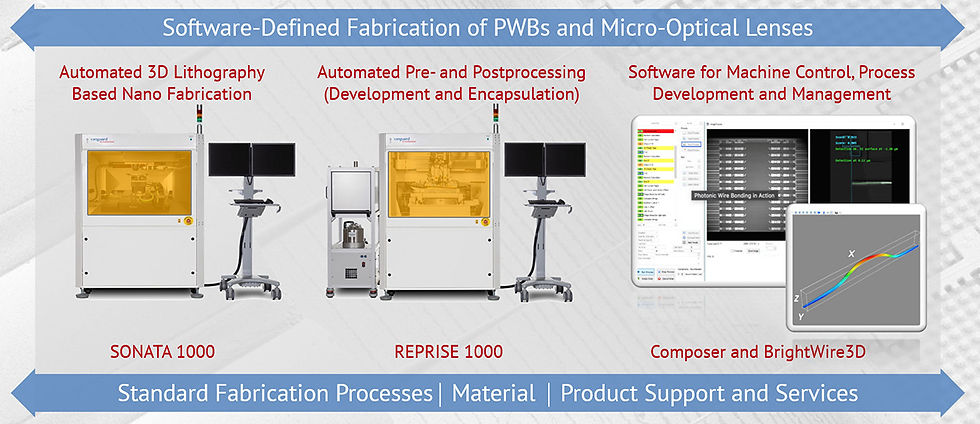
Note: It comprises the automated 3D lithography-based nano fabrication unit Sonata 1000 and the automated pre- and postprocessing unit Reprise 1000. The systems are equipped with Vanguard’s BrightWire3D software, enabling highly precise detection and on-the-fly trajectory calculations. Vanguard’s own photoresists (Vanguard VanCore series), standard process development, as well as product support and engineering services complete Vanguard’s solution from prototyping to high-volume production.
Streamlining Diverse Photonic Integration
Integrating various photonic components from different material systems poses challenges. Hybrid modules may combine lasers, amplifiers, silicon/nitride passives, lithium niobate devices, and specialty fibers. Vanguard’s solutions address the complex integration needs arising from diverse optical properties and materials. Faceted elements and precision PWB alignment reduce coupling losses for optimal light transfer between components. Reliable, reproducible processes ensure cost-effective manufacturing.

Expanding Production for Next-Generation Applications
Vanguard has expanded adopters across datacom, telecom, AI, quantum tech, and other advanced domains. Customers utilize PWB and faceted elements to enable hybrid integration and solve packaging problems. Compatibility with foundry processes avoids converter requirements. Relaxed alignment tolerances facilitate passive assembly. Vanguard also streamlines incorporating solutions into manufacturing chains to boost production efficiency.

Enabling Cutting-Edge Photonic Applications
PWB has been applied for advanced applications like self-locked Kerr soliton microcombs, sub-100 Hz lasers, and ultra-low temperature quantum photonics experiments. Faceted elements have improved efficiencies for high-bandwidth modulators and sensors. The technology provides scalable beam shaping for LiDAR, increases detector collection areas, and overcomes nanophotonic design limitations.

Conclusion
Vanguard Automation delivers an integrated portfolio of technologies to unify diverse photonic platforms. Photonic Wire Bonding combines component strengths for high-performance multi-chip modules. Faceted elements enable wafer-scale probing. With automated, reliable solutions, Vanguard is powering next-generation photonic integration and manufacturing.
Comments